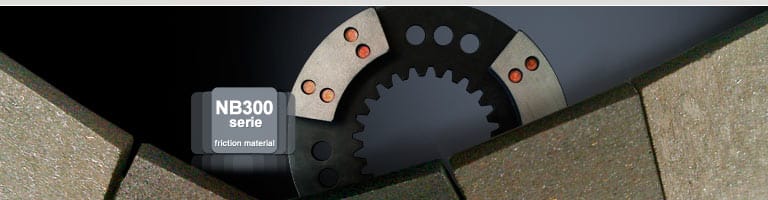
ORGANIC BASED FRICTION MATERIALS
Automotive and Industrial Applications
In this friction material family all those lining compounds are listed which base on rubber and synthetic resin to bind together their ingredients. Friction modifying agents, such as fibres, metal particles or fillers, are embedded in the organic binder matrix and form by interacting in numerous combinations a great variety of friction material composites with their very own unique friction and comfort characteristics.
Focused on the optimum integration of brake linings and clutch facings into your industrial environment, the friction materials are adjusted to each particular application’s requirement or they will be newly developed, as the case may be. The available friction materials, reliant upon material compound and formulation, cover the whole spectrum of common applications: ranging from low to high coefficients of friction of over µ = 0.5. The product range varies from softer lining materials (for lower normal force between both friction partners) up to harder friction materials like the ones for disc brake pads.
ROLL LINING MATERIALS – UNIVERSAL
Flexible roll linings can be supplied as blank segments or as 10m strip rolls for (re)-lining backing supports, such as brake shoes and brake bands. The roll linings will be manufactured in chosen width, length and thickness, drilled/ non-drilled, with/ without side markings, with/ without chamfered ends or with/ without applied adhesive. Does the custom application require high strength of the friction material and great temperature resilience, the best chosen friction material would be woven roll lining material. The products can be supplied furthermore in configurations which feature resistance to oil or seawater.
1) roll linings mass-moulded with wire backing
2) roll linings mass-moulded without wire backing
3) roll linings of woven material
SHEET LINING MATERIALS – UNIVERSAL
The machining process supports the production of sheet lining materials in response to various custom specific requirements according to hardness grade, coefficients of friction and desired wear characteristics. Iron-free and steel-free compounds are, in addition, resistant to corrosion; non-magnetic and non-magnetizable materials do not contain any metal fibers. Sheet linings provide a particular “shock strength”, if they are press moulded out of woven pre-processing fabrics.
1) flat sheets press moulded (flexible up to rigid)
2) flat sheets of woven material
3) sliding materials in sheets
FRICTION MATERIALS WITHOUT BACKING SUPPORT – CONTOUR CONFORM
Going through punching, turning, or water jet cutting processes, rings and discs in various dimensions will be manufactured out of hot press moulded sheets or woven clutch facings with functional division (multi-layer). According to application the items will be supplied in drilled, grooved and various marking options. In addition to shaping out of sheet or roll lining materials through mechanical processing (cutting process), further methods in press moulding and contour-conform injection moulding are in use (shaping process). This is resulting in friction materials with particular high mechanical strengths.
1) friction disc rings, clutch facings, discs
2) segments (pads), pucks (pads), friction pads, cones, friction blocks
DRUM BRAKE LININGS – CONTOUR CONFORM
The production with single nest tools or half-shell tools is based on lot size and custom application, or rely otherwise on further processing of hardened roll lining materials. According to a large number of application formats we are equipped with a high quantity of friction material compounds.
1) in various length, width, thickness and radius
2) in various options: drilled/ non-drilled, chamfered, marking at the edges, coating of inner wall
FRICTION MATERIALS WITH BACKING SUPPORT – CONTOUR CONFORM
Contour conforming friction materials will be joined onto the backing support through adhesive bonding and curing processes. Since only the entire contact between the surfaces guarantees good shear levels, uniform pressure distribution and long lifespan. Depending on application the lining spectrum from which to choose varies: from soft bendable materials for exact fit, over flexible ones hardend to radius, to harder friction materials. In doing so, material consistency of counter-surfaces needs further attention while selecting.
1) friction discs, clutch discs
2) brake shoes, brake bands
3) cones, segments (pads), clutch buttons
DISC BRAKE PADS – CONTOUR CONFORM
The disc brake pads are strongly bonded to backing plates (metal support), made of steel, cast or forging. Brake pad moulding, which means joining of backing plate and friction material under pressure, time and temperature, is always carried out in contour-designed mould cavities according to defined processing instructions. Those are adapted to requirement, dimension and handled mixture.
1) in various linings: parallel lining, segment lining, pad grinded to width, true positive moulded
2) in various options: recesses, slots / grooves, run-in chamfers
3) in various backing plates: steel, cast or forging
DEVELOPMENT / PRODUCTION – FORMULATIONS
1) Development of friction material (customer supporting projects)
2) Implementation of the engineered lining compound into production
3) Manufacturing of mixtures
4) Distribution of raw materials
Materials
NB100
NB101
NB102
NB103
NB104
NB107
NB108
NB200
NB201
NB202
NB300
NB301
NB302
NB303
NB304
NB305
NB306
NB307
NB308
NB309
NB310
NB311
NB312
NB313
NB314
NB315
NB400
NB401
NB402
NB406
NB500
NB501
NB502